Application of SGNR Tightening System
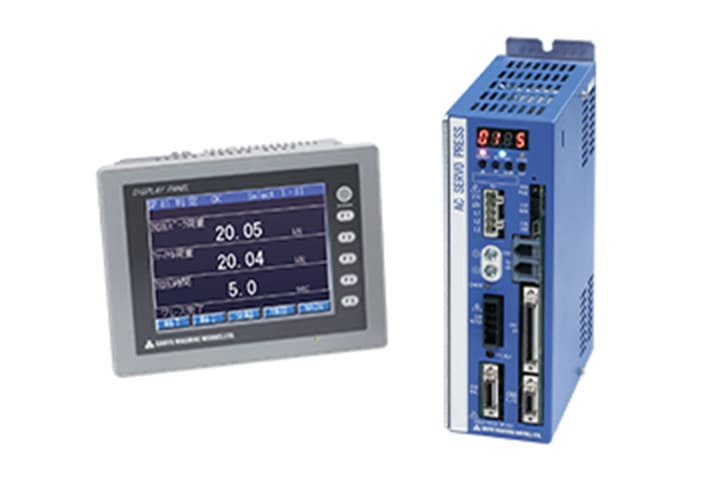
Advantages of the SGNR Tightening System
The SANYO SGNR tightening system is applied in assembly production lines in industries such as automotive and electronics, for example, in the bolting of automotive engines, chassis, and the assembly of electronic devices. It can perform both tightening and loosening of bolts. The SGNR tightening system is widely used in well-known companies like Changan Mazda, in conjunction with automatic nail feeding machines and general-purpose robots, to achieve automation in automotive production lines. Its high precision ensures that the bolts of internal automotive parts are tightened accurately, improving the product qualification rate.
Application in Automotive Production Lines
The SGNR tightening shaft can be installed at the front end of general-purpose robots, in conjunction with automatic nail feeding machines for automotive assembly, such as the Kawasaki robots on the Changan Mazda production line. The tightening system can communicate and transmit data with Mitsubishi PLC or other industrial control devices through DeviceNet, EtherNet, and CCLink communication protocols. The PLC issues control commands, selects program numbers and parameter numbers according to process requirements, and works with automatic nail feeding machines and robots to complete the actions of picking nails and tightening bolts. SGNR sets the nail picking confirmation program to ensure that the bolt tightening machine grabs the bolts, and the actions of picking nails and tightening are performed on the same tightening shaft. One driver can set up to 8 tightening programs and 32 sets of tightening parameters, allowing the same tightening shaft to achieve different target torques. The pre-tightening setting allows the tightening shaft to first pre-tighten at low speed for 1 second to ensure accurate initial alignment; the maximum angle detection during tightening can avoid idling of the tightening shaft caused by position deviation, ensuring that the bolts are tightened properly. A set of tightening systems can configure up to 32 tightening shafts, with any model selected. In automotive production lines, robots are generally equipped with 2 to 4 tightening shafts. UIT software and DP series touch screens can set and display tightening data, which can be saved and sent to monitoring software for traceability and real-time monitoring of the automotive tightening process.
Application in Automotive Production Lines
Application in Equipment Assembly
The SGNR tightening shaft can also be applied in the assembly of small and medium-sized electronic products, such as multi-axis automatic bolt tightening machines. Parameters are set according to process requirements.When the device receives a tightening command, the driver of the tightening shaft first pre-tightens to confirm the position, and then tightens the bolt. During the tightening process, sensors continuously detect the tightening position and torque of the bolt, and feedback the detection results to the control unit. The control unit adjusts the speed and torque of the tightening shaft based on the feedback results to achieve the best tightening effect. The tightening program can be set to be interlocked, terminating the program operation in case of tightening NG or mechanical failure.
Application in Equipment Assembly
Previous Page:
recommend News
Hydraulic System Design and Manufacturing Expert: Creating a Stable and Efficient Power System