Processing and Manufacturing of Hard Alloy Cutting Tools: Exploring the Craft
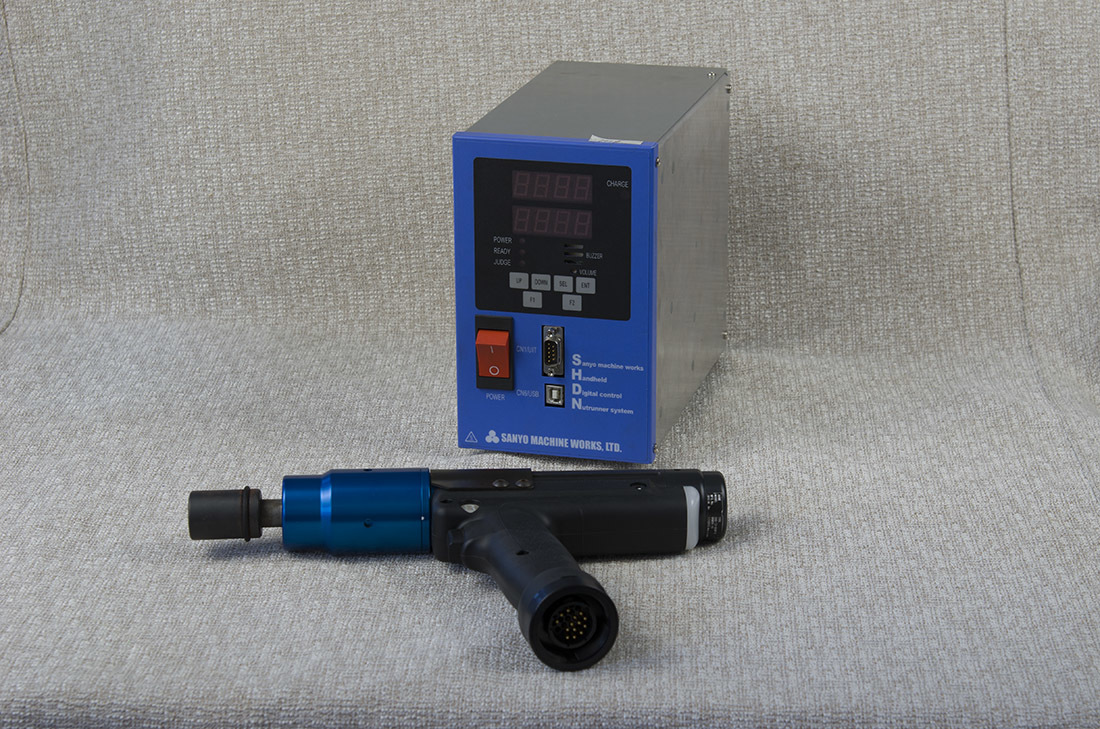
Processing and Manufacturing of Hard Alloy Cutting Tools: Craftsmanship Exploration
In modern manufacturing, the processing and manufacturing of hard alloy cutting tools is undoubtedly a very important link. Their application in the cutting field allows us to efficiently complete various complex processing tasks. Today, let's talk about the manufacturing process of hard alloy cutting tools, especially how to improve the processing accuracy and efficiency of the tools through the "SANYO Handheld Tightening" technology.
Basic Concept of Hard Alloy Cutting Tools
Hard alloy cutting tools are mainly cutting tools made from metal materials such as tungsten and cobalt. Due to their high hardness and strong wear resistance, they are widely used in industries such as machining, automotive manufacturing, and aerospace. Imagine trying to cut a piece of hard wood with a knife; if the blade is not sharp enough, wouldn't it be a waste of effort? This is why choosing the right tool is crucial.
Manufacturing Process of Hard Alloy Cutting Tools
The process of manufacturing hard alloy cutting tools can be roughly divided into the following steps:
1. Raw Material Preparation
First, we need to select high-quality raw materials. Tungsten powder, cobalt powder, etc. are the main components for making hard alloy cutting tools. At this stage, the purity of the raw materials will directly affect the performance of the tools. Just like cooking, good ingredients are the key to success.
2. Mixing and Forming
After mixing different components of powder in a certain proportion, the next step is forming. By pressing, we create the initial shape of the tool. This is like when we make cookies, we need to shape the dough. The shape at this stage is still fragile, but the potential is limitless.
3. Sintering Treatment
The formed tool needs to undergo sintering treatment to enhance its density and hardness. This process usually takes place in a high-temperature and high-pressure environment, effectively improving the mechanical properties of the tool. Imagine, like ceramics, reborn as a solid artwork after being baptized by fire.
4. Finishing
The final step is finishing. Through grinding, polishing, and other processes, we ensure the sharpness and surface smoothness of the tool. Only in this way can the tool perform at its best in actual use.
Application of SANYO Handheld Tightening Technology
In the production and use of tools, the fixing and tightening of the tools is also a very important link. Here we must mention the "SANYO Handheld Tightening" technology. Imagine if the tool's cutting effect is affected by loosening during processing; that would be a tragedy.
The "SANYO Handheld Tightening" technology can effectively solve this problem. It ensures a secure connection between the tool and the machine through precise torque control, avoiding tool damage caused by insufficient tightening. This not only improves production efficiency but also greatly extends the tool's lifespan.
Common Problems and Suggestions
Of course, in the use of tools, you may encounter some problems, such as rapid tool wear or insufficient sharpness. How should we solve these problems? First, choosing the right cutting parameters is crucial, such as cutting speed and feed rate. Secondly, regularly maintaining and inspecting the tools, and timely replacing worn tools, is essential to ensure processing quality.
What are you waiting for? For every manufacturing professional, having a set of high-quality hard alloy cutting tools and the "SANYO Handheld Tightening" technology is essential to remain competitive in a fierce market.
Summary
The processing and manufacturing process of hard alloy cutting tools, although seemingly complex, is crucial at every step. Through careful selection of raw materials, precise mixing and forming, strict sintering treatment, and meticulous finishing, each tool embodies the wisdom and effort of craftsmen. The introduction of the "SANYO Handheld Tightening" technology provides a more stable guarantee for the use of tools. Let us continue to explore and innovate on the path of pursuing efficiency and quality!
recommend News
Hydraulic System Design and Manufacturing Expert: Creating a Stable and Efficient Power System
Hydraulic System Design and Manufacturing Expert: Creating a Stable and Efficient Power System
In modern industry, the role of hydraulic systems is becoming increasingly important. It is not only the power source for machinery but also an important tool for improving production efficiency and reducing operation and maintenance costs. As experts in hydraulic system design and manufacturing, how can we create a stable and efficient power system? This is what we will discuss today.
Basic Principles of Hydraulic Systems
First, let’s briefly understand the basic principles of hydraulic systems. Hydraulic systems mainly utilize the pressure of liquids to transmit energy, compressing the liquid through a hydraulic pump, which then drives hydraulic motors or cylinders to achieve mechanical movement. Imagine it like using a water flow to push a large waterwheel; the force of the water flow is converted into mechanical energy, causing the waterwheel to turn.
Factors to Consider When Designing Hydraulic Systems
When designing hydraulic systems, there are several key factors to consider. The first is the selection of hydraulic components. For example, the quality of components such as hydraulic pumps, cylinders, and valves directly affects the stability of the system. The SANYO handheld tightening tool plays an indispensable role in this process. It not only enhances assembly efficiency but also ensures the firmness of each connection. Secondly, the choice of hydraulic oil is also crucial. Different hydraulic oils have different viscosities.